Die Firma Johann Düro GmbH & Co. KG baut seit über 140 Jahren nahe der Ortschaft Taben-Rodt im Steinbruch Düro das Hartgestein Quarzit ab und verarbeitet diesen mit modernster Aufbereitungstechnik zu Zuschlagstoffen für Asphalt und Beton, Gleisschotter, Wasserbausteinen und Tragschichtgemischen für den Straßenbau.
Aber auch unter Einsatz dieser modernen Aufbereitungsanlagen fallen im Rahmen der Produktion „Kuppelprodukte“, wie Vorsieb und füllerreiche Brechsande, an, die in der Regel kaum zu vermarkten sind und auf dem Steinbruchgelände deponiert werden. Bis zu 15 % der Gesamtproduktion waren in der Vergangenheit nicht verwertbar.
Ziel des Projektes „Integrierung einer Nassaufbereitungsanlage in den bestehenden Produktionsprozess eines Natursteinwerks“ war und ist die Aufbereitung dieser Kuppelprodukte zu hochwertigen Bau- und Zuschlagstoffen, verbunden mit einer deutlichen Steigerung der Ressourceneffizienz.
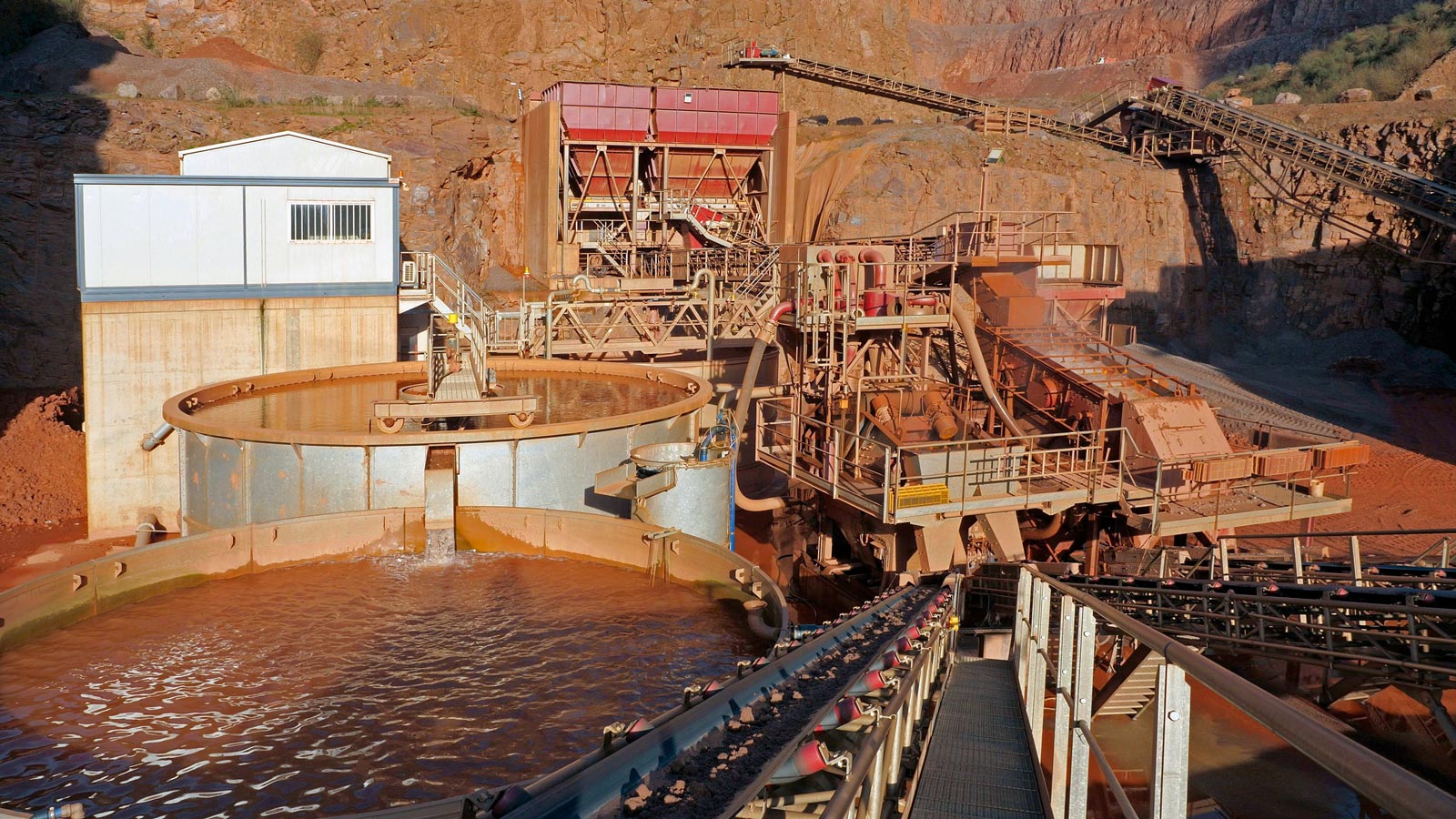
Zur Sicherstellung einer möglichst flexiblen Zuführung verschiedener Materialien wurden dabei mehrere Aufgabemöglichkeiten auf die Nassaufbereitung realisiert. Das im laufenden Produktionsprozess anfallende Vorsiebmaterial wird ohne Zwischentransporte automatisiert über Bandanlagen der Nassaufbereitung zugeführt. Die Aufgabe von Kuppelprodukten aus der Nachbrechanlage und Beständen von Althalden wird über separate Aufgabetrichter sichergestellt.
Mit Wasch- und Entwässerungssiebmaschinen in Verbindung mit Hydrozyklonen werden die Feinstkornanteile von den aufgegebenen Materialien abgewaschen. Weiterhin erfolgt eine Absiebung in verschiedene Kornklassen. Aus ehemals nicht zu vermarktenden Produkten entstehen im Rahmen dieses Prozesses hochwertige gewaschene Splitte und Brechsande. In der Prozesswasseraufbereitung wird das Waschwasser durch Sedimentation geklärt und im Kreislauf dem Waschprozess wieder zugeführt. Die sedimentierten Feinstbestandteile werden als homogenisierter Schlamm einer Kammerfilterpresse zugeführt. Der Schlamm wird entwässert und als sogenannter Filterkuchen ausgetragen. Dieses Produkt, per Definition ein Ton, wird in die keramische Industrie vermarktet.
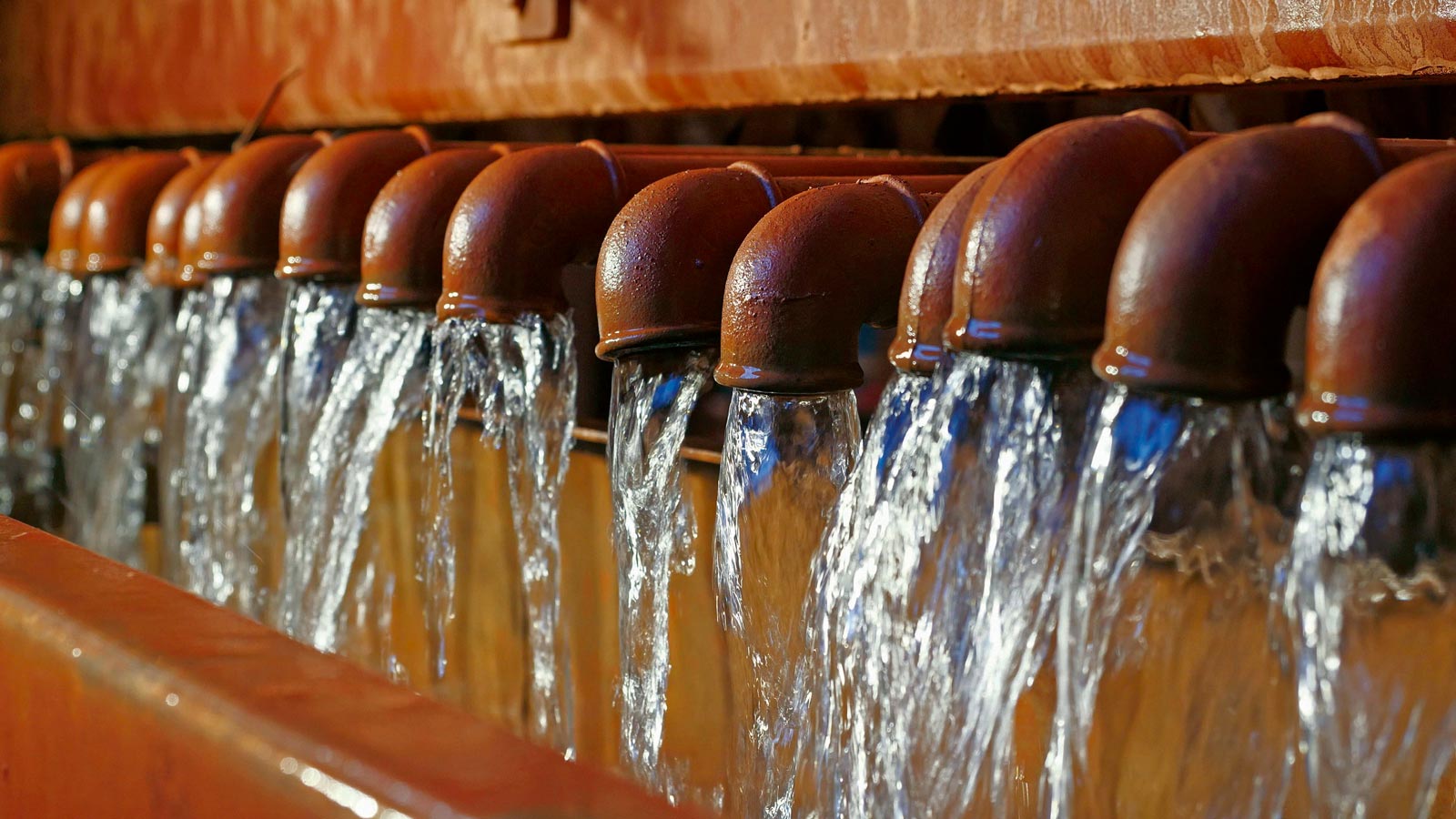
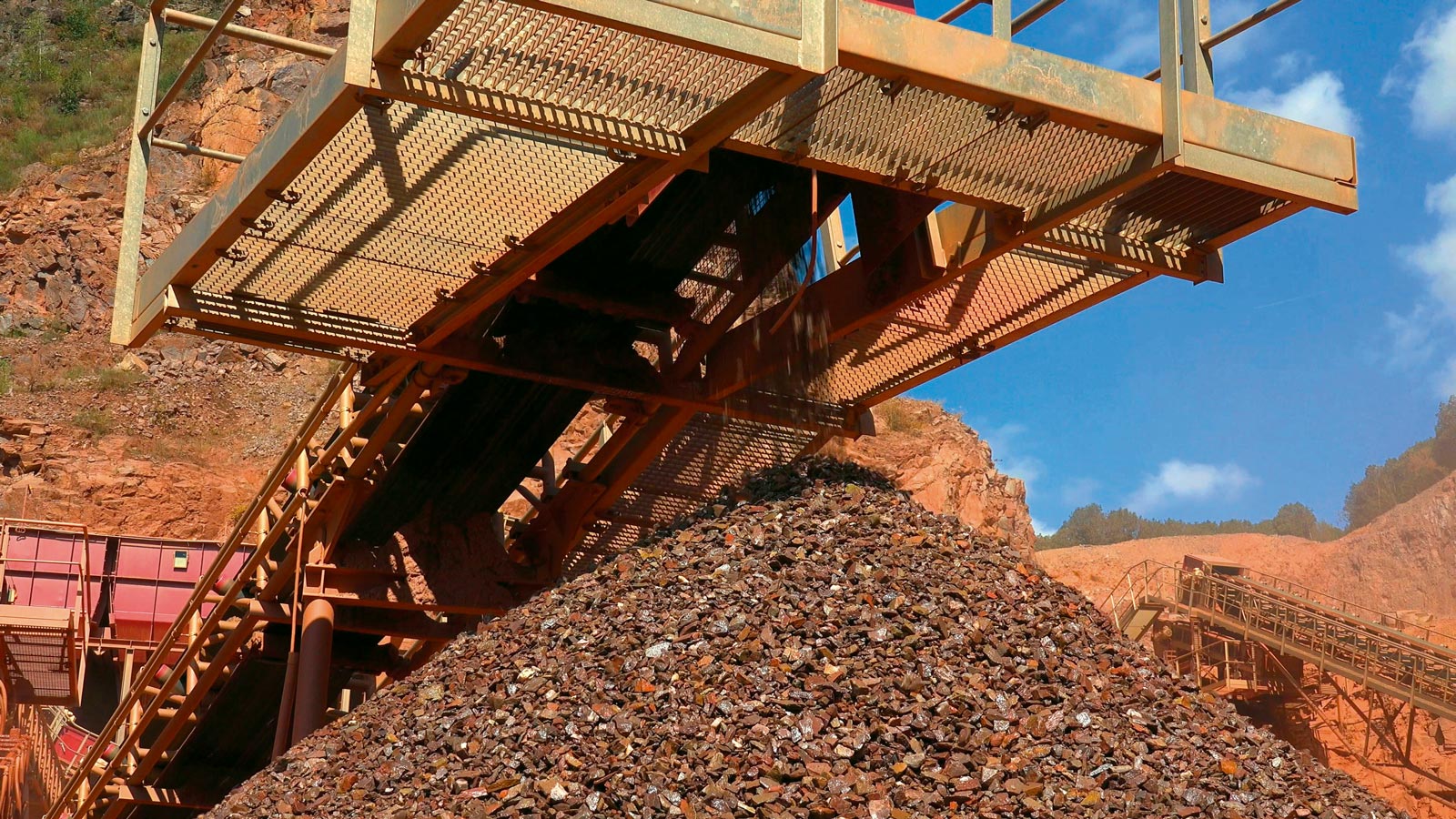
Nach einer dreijährigen Betriebszeit und einer aufbereiteten Menge von ca. 600.000 t zeigt sich eine dauerhafte Steigerung der Ressourceneffizienz auf annähernd 100 Prozent. Nahezu die komplette Abbaumenge wird aufbereitet und in qualitativ hochwertige Anwendungsbereiche vermarktet. Die Steigerung der Ressourceneffizienz führt bei gleichbleibender Verkaufsmenge zu einer deutlichen Reduzierung der Gesamtproduktionsmenge und folglich zu einer Reduzierung des Energieeinsatzes und einer Verringerung der Emissionen. Die Betriebsdauer des Steinbruchs wird bei gleichzeitig sinkendem jährlichen Flächenverbrauch verlängert. Die Steigerung der Wertschöpfung verbessert erheblich die Wettbewerbsfähigkeit und führt somit auch zu einer nachhaltigen Sicherung der Arbeitsplätze.
Preisträger im Deutschen Nachhaltigkeitspreis 2022 mit diesem Projekt:
Johann Düro GmbH & Co. KG
Korzerter Straße 18
42349 Wuppertal
www.duero.biz